Environment
Apple 2030 A plan as innovative
as our products.
And designing products you love. Apple 2030 is our plan to do both.
A detailed approach.
-
Design our products with recycled and renewable materials.1
Our Approach
Recycled and renewable materials often carry a lighter footprint than mined materials. By sourcing more recycled and renewable content, we can help to one day end our reliance on mining.
Our Progress
22% of the materials we shipped in Apple products came from recycled and renewable sources.2
-
Source all manufacturing electricity from clean energy.
Our Approach
Most of our carbon footprint comes from the electricity used to manufacture our products. So our suppliers are transitioning to electricity generated from solar, wind and other renewable sources.
Our Progress
Over 320 of our suppliers have already committed to using 100% renewable electricity by 2030.3
-
Package and ship our products with less emissions.
-
Match 100% of our products’ energy use with clean electricity.6
Our Approach
We’re investing in global renewable energy projects that help address the electricity our products use. And we’re making these devices even more energy efficient.
Our Progress
We’re matching 100% of the expected electricity use for Apple Watch models by investing in projects like the IP Radian Solar project.7
-
Maximise the materials we recover from recycled products.

Our progress by the numbers.
We introduced our most significant product emissions reductions to date with the 2023 Apple Watch line-up.10
Over 55% reduction in CO₂e emissions across our carbon footprint since 2015.
18.5M tonnes of CO₂e emissions avoided through our Supplier Clean Energy Programme in 2023.
22% of materials shipped in our products came from recycled and renewable sources in 2023.
12.8M devices and accessories sent to new owners for reuse in 2023.
20% reduction in product transportation emissions compared to 2022.
The proof is in our products.
The same innovative thinking that goes into creating the products you love goes into our environmental initiatives. And as we design our products, we’re also using smarter chemistry to make sure they’re safer for everyone who assembles, uses and recycles them.
Partnerships that do a world of good.
Doing right by the planet means doing right by the people who live on it — especially those most impacted by environmental risks. So we’re supporting partners and communities worldwide. Because we can achieve more together than we can alone.
Help make
Mother Nature proud.
There are many small actions you can take to make a big difference for the planet.
Trade in your
device for credit.
Or recycle it for free.
It’s good for you and the planet.

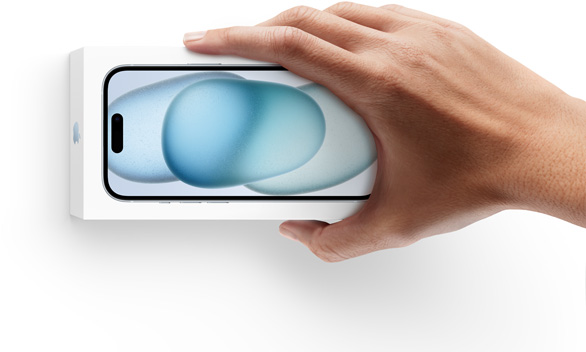
Designed with the earth in mind.
Learn more about the progress of your Apple devices with our product environmental reports.
An even closer look at our progress.
Learn more about our latest efforts to fight climate change and support equity.
View the 2024 Environmental Progress Report (PDF)Additional Reports and Resources
Circular Economy
Our aim is to make products using only recycled or renewable materials — so we prioritise, responsibly source and recover materials.
- Learn how we prioritise materials with our Material Impact Profiles (PDF)
- Read our white paper on Apple’s Paper and Packaging Strategy (PDF)
- Read our Responsible Fiber Specification (PDF)
- Read our white paper on expanding access to service and repairs (PDF)
- Learn how to trade in or recycle your device
- Learn more about disassembly for professional recyclers
Smarter Chemistry
Apple has a rigorous programme to ensure the safety of chemicals used in our products. Learn about Apple’s strict standards, diligent toxicological assessments and methodology for assessing chemicals of concern.
- Read the Regulated Substances Specification (PDF)
- Read our white paper on Integrating Toxicological Assessments in Material Selection for Apple Products (PDF)
- Read our Protocol for Prioritising Chemicals of Concern in the Electronics Industry (PDF)
- Read about Apple’s commitment to phasing out per- and polyfluoroalkyl substances (PFAS) (PDF)
Climate Change
Climate change is a defining issue of our time. View detailed updates on our progress.
People and Environment in Our Supply Chain
We hold ourselves and our suppliers to the highest standards of labour and human rights, health and safety in the workplace, environmental practices, and the responsible sourcing of materials.
Frequently Asked Questions
Find answers to common questions about Apple and the environment.
More from Apple on the environment.
Our values lead the way.
-
Accessibility
Our built-in accessibility features are designed to work the way you do.
-
Privacy
We design every product and service to keep your data safe and secure.
-
Supply Chain Innovation
We prioritise providing safe, respectful, supportive workplaces for everyone.
-
Education
We empower students and educators to learn, create and define their own success.